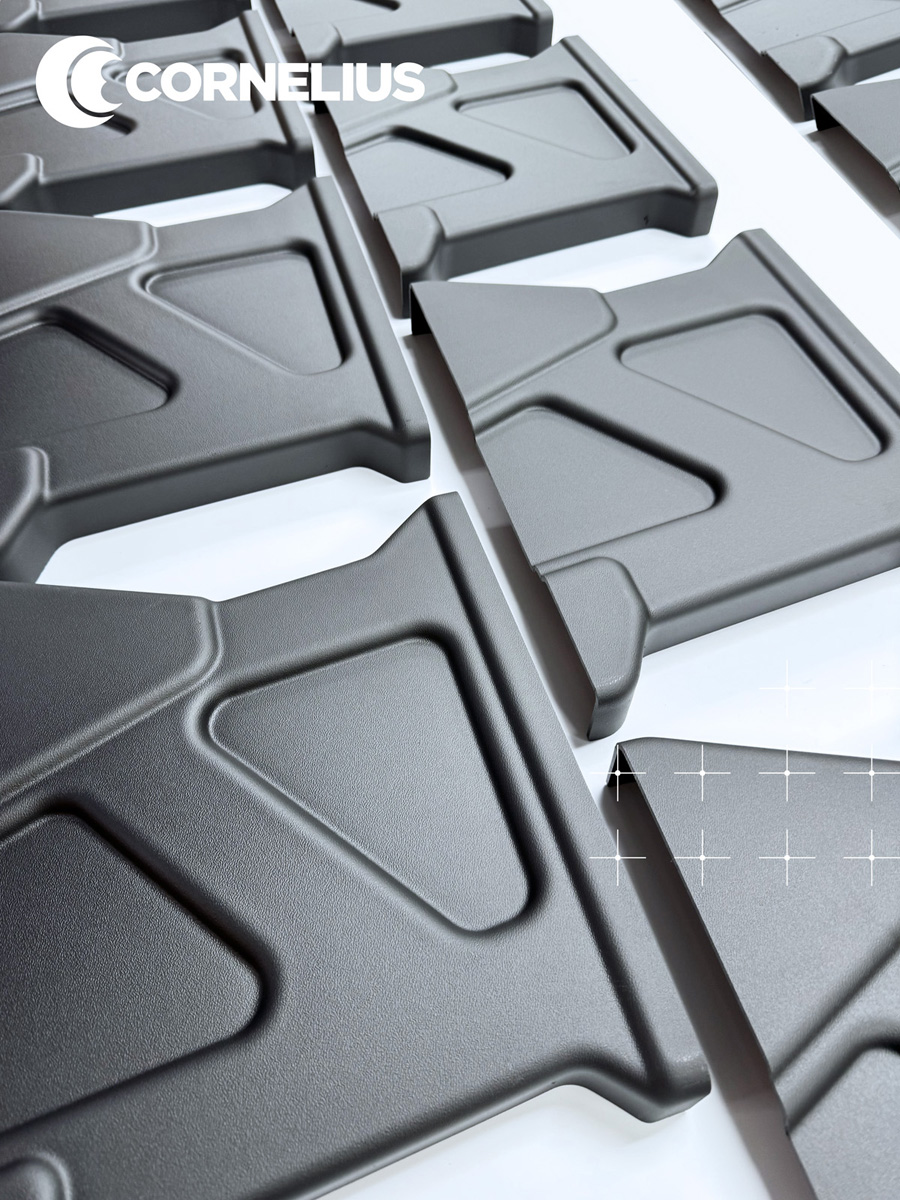
Vacuum forming is a highly flexible and economical manufacturing process that shapes plastic sheets into a wide range of products, including packaging, vehicle panels, medical equipment, and retail displays. The process involves heating a plastic sheet, forming it over a mould, and using vacuum pressure to achieve the desired shape.
Key Steps:
– The plastic sheet is heated until soft.
– It is then placed over a mould.
– A vacuum pulls the sheet tightly around the mould.
– The part is cooled and trimmed to size.
Common Materials:
Materials like ABS, acrylic, APET, HIPS, HDPE, PETG, polypropylene, PVC, and ASA are commonly used, each offering distinct advantages for different uses.
Advantages:
– Lower tooling costs than injection moulding.
– Rapid prototyping and short lead times.
– Suitable for both small and large parts.
– Flexible for low or high-volume production.
Applications:
Vacuum forming is used in many sectors, including automotive, medical, aerospace, packaging, and retail, due to its adaptability and efficiency.
Cornelius provides advanced vacuum forming with CAD/CAM precision, scalable UK production, and decades of expertise for reliable, high-quality results.